Research background
Humidity sensitive materials are generally used as humidity sensors. It uses the adsorption effect to directly adsorb water molecules, so that its surface conductance or body dielectric properties and other physical properties change, so as to detect one of the important physical quantities in the human living environment - humidity. The most common representation of humidity is relative humidity (RH%). The development history of temperature sensors began in the 1930s, represented by resistive sensors made of lithium chloride (LiCl) electrolytes. Subsequently, in terms of moisture sensing materials, it can be roughly divided into three categories: electrolyte type, semiconductor ceramic type and organic polymer type. The organic polymer type can be divided into capacitance type and resistance type according to its structural characteristics. Humidity sensor generally has the shortcomings of not ideal stability and reliability, poor moisture resistance, and weak anti-interference ability, which have restricted and hindered its practical application and further development for many years. Therefore, the exploration of new high-precision, high-reliability and long-life humidity sensing structural materials, the study of the drift mechanism of various humidity sensors, and the improvement and improvement of its stability and reliability have aroused great attention and interest of scientists from various countries, which has become the key to the further development of humidity sensors.
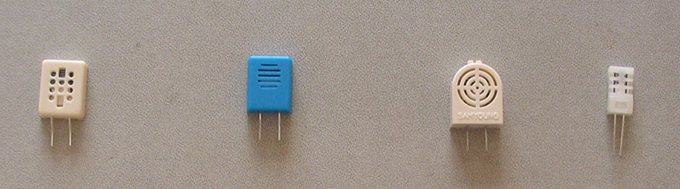
Abroad, since the advent of the electrolyte resistance type humidity sensor represented by LiCl in the 1930s, new humidity sensitive materials have been emerging, which has greatly promoted the development of humidity sensors.
In 1938, Dunmore of the United States was the first to make an electric humidity sensor with PVA (polyvinyl alcohol) and LiCl mixture as a moisture sensing film, which was successfully used in radiosonde. However, it has some disadvantages such as narrow range, easy erosion under high humidity, troublesome maintenance and short service life.
In 1954, the polymer capacitive humidity sensor using butyl cellulose acetate as humidity sensing material was developed successfully
In 1955, MartinPope of the United States developed a polymer resistance humidity sensor with polystyrene sulfonic acid ion exchange resin (PSS) as a humidity sensing material, but the wet hysteresis difference is large and the long-term stability is not good.
In 1966, inorganic materials such as Fe2O3 and Al2O3 were used as humidity sensitive materials, resulting in a new class of ceramic humidity sensors. It can detect humidity at high temperatures, but it is vulnerable to pollution and has poor stability.
A new shrinkable humidity sensor appeared in 1969. The hygrosensitive material used is composed of graphite dispersed in a high molecular hygroscopic resin. Its humidity range is large, the resistance value is also low, but the low humidity sensitivity is poor, and the pollution is serious, it is difficult to eliminate the hysteresis phenomenon.
In 1975, the resonant quartz vibrator humidity sensor based on polyimide (PI) was developed.
From 1976 to 1978, Tsuneji Nieda and others in Japan developed MgCrO4-TiO2 and other ceramic humidity sensitive materials. The method of heating cleaning is adopted to solve the stability problem, and it is applied to automatic microwave oven. Polymer humidity sensors are commercialized.
In 1982, polyimide (PI) was applied to capacitive humidity sensor, which has the characteristics of high temperature strength, good dielectric stability and strong resistance to chemical corrosion.
Domestic research began in the early 1960s, mainly for semiconductor ceramic humidity sensors.
In 1990, Wang Tianbao et al., Shanghai Institute of Ceramics, and Xu Tingxian et al., Tianjin University, respectively developed high performance humidity sensors using bismuth sodium potassium titanate compact ceramics and nickel-zinc ferrite compact ceramics, and systematically studied their conductive mechanism.
In 1991, Shanghai Jiao Tong University and Huazhong University of Science and Technology developed a membrane sensor with good stability and fast response using sol-gel micro-powder technology.
In 1991, Gu Changzhi and others of Jilin University made a sulfonated copper phthalocyanine resistance humidity sensor by using LB film technology.
In 1993, Luo Rufang et al. of Shanghai Silicate Institute developed PI capacitive humidity sensor.
1995 Beijing University of Chemical Technology Chen Yichi et al. grafted HMPTAC onto polyethylene (PE) film and obtained a hygrosensitive film with excellent water resistance and long-term stability. Soaking in water for more than two hours, the humidity sensing characteristics remained basically unchanged.
In 1996, Mujie Yang of Zhejiang University and Casalbore-Miceli of the Italian Academy of Sciences cooperated to develop sulphate-doped polypropargyl alcohol humidity sensitive material.
In recent years, the research of hygrosensitivity mainly focuses on the development of new hygrosensitive materials and the research of humidity resistance/humidity sensing of chemical and photoelectric devices.
Canonical study
Material research of humidity sensor, usually on ceramic or silicon substrate, through spinning coating, lifting, manual titration method, the moisture sensing material is deposited on the substrate surface of the finger electrode, through the impedance measurement at different humidity analysis of the material's humidity sensitive characteristics. It should be noted that the humidity sensitive analysis is based on the dissociation of water molecules on the surface of the material, so the measurement can only be made using an impedance analyzer, not a DC electrical analyzer.
Among all kinds of humidity sensitive materials with new morphology and structure, one-dimensional materials show good performance in response recovery speed, which can be at the level of a few seconds or even milliseconds, which is unmatched by traditional polymer or particle humidity sensors.
Gas sensitive, photoelectric and other devices, under different humidity, water molecules adsorption will cause performance impact, so the research of moisture resistance/humidity characteristics of the device is a necessary part of the industrialization of relevant functional materials/devices. Especially in recent years, with the continuous upgrading and improvement of humidity generation equipment, it is possible to control various atmospheres and humidity at the same time, as well as humidity control at high temperatures, so relevant research has received a lot of attention.
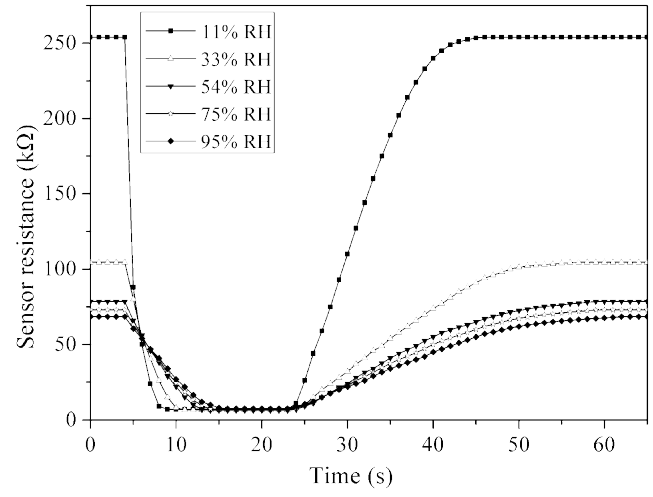
Traditional humidity sensors are mainly concentrated in more than 10% RH, mainly because low humidity environmental control is difficult to achieve. Now through the continuous evaporation of water molecules, humidity above 10 ppb can be achieved continuously. This kind of ultra-low humidity sensor has great application in semiconductor, chemical synthesis, medical and other fields, and has a good development prospect.
Equipment recommendation
The research of humidity sensor needs electrical measurement system and environmental control system, which mainly measures impedance change. The atmosphere control involves saturated salt solution generator, dual-flow humidity generation system, ultra-low humidity distribution gas-liquid distribution system, etc.
1. Measuring equipment
a. CHS-1 intelligent humidity sensitive analysis system: It is mainly used for complex impedance scanning, wet hysteresis analysis, complex impedance spectrum analysis and other functions at different frequencies. The system has the characteristics of high measurement accuracy, fast measurement speed and high intelligence. It can be used for humidity sensitive analysis of various nanomaterials, pore materials, powder/particle materials, bulk materials, semiconductors, carbon tubes, organic materials, etc.
2. Environmental control equipment
A. Saturated salt solution generator: Through saturated salt solution to achieve a fixed humidity value of the environment, common such as: LiCl corresponding to 11% RH; MgCl2 corresponds to 33% RH; Mg(NO3)2 corresponds to 54% RH; NaCl corresponds to 75% RH; KCl corresponds to 85% RH; KNO3 corresponds to 95% RH. This method is simple and convenient, but the generated humidity value is affected by the ambient temperature, the geometry of the solution bottle, the height of the solution, etc., especially in the process of opening the bottle cap and inserting the device under test, the target humidity environment will be exchanged with the air outside the bottle, so the error value is usually above 10%RH.
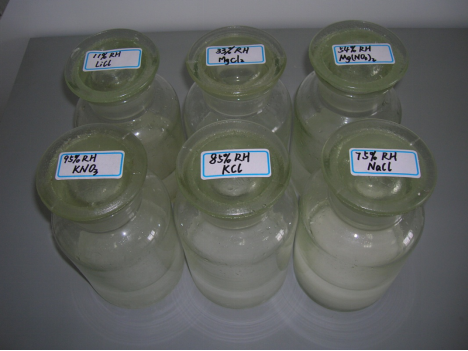
b. DHD-II dual-flow humidity generation system: It can provide a high precision humidity atmosphere (2%~95% RH) at a certain temperature (10~40°C). The system provides various humidity atmospheres required for device humidity sensitivity test through dynamic airflow. The system consists of main engine, wet chamber, wet/dry gas emitter and so on. According to the set humidity value, the system automatically adjusts the flow rate and proportion of wet and dry gas, and configures a high-precision humidity atmosphere. The system can adjust the desired temperature range at the same time, and configure a high-precision humidity atmosphere at different temperatures, which can provide the required experimental atmosphere for analyzing the characteristics of humidity sensors or humidity sensitive materials.
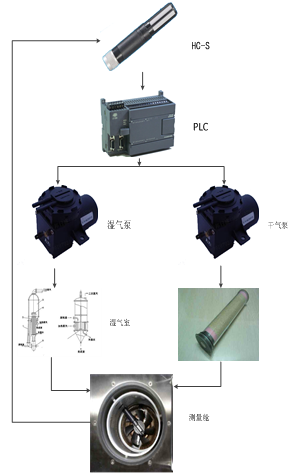
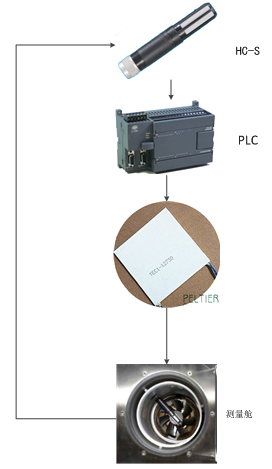
The process of humidity control is shown in the figure above (left). First, the HC-S probe is used to measure the humidity and the humidity signal is sent to the PLC controller, which determines humidification or dehumidification according to the humidity signal. Humidification is provided by the humidifier, dehumidification is provided by the dryer, and gas circulation is promoted by the air pump, and finally an accurate and stable humidity atmosphere is obtained.
c. DGL-III Humidity control gas-liquid distribution system: suitable for the dynamic distribution of all kinds of gas sources (such as NOx, H2S, CO, etc.) or liquid sources (such as alcohols, benzene, organic amines, ethers, ketones and other volatile liquids). The humidity control module configured in the system can be used to control the humidity independently or configure various gases with different humidity. The principle of moisture control: The background gas is divided into two channels, both of which are controlled by MFC with high precision and fast response, and the total flow rate of the background gas for moisture control is set. While maintaining the flow rate and constant, the two channels of gas are dried by molecular sieve as dry gas path, and the other is dried by liquid generation device as wet gas path. The system adopts PID algorithm to quickly adjust the velocity ratio of the two channels of gas. Combined with the real-time monitoring and feedback of the high-precision temperature and humidity sensor, the background gas with a certain flow rate of specific humidity is finally obtained. The background gas can be mixed with the target gas in a certain proportion to finally obtain the target gas with a certain humidity.
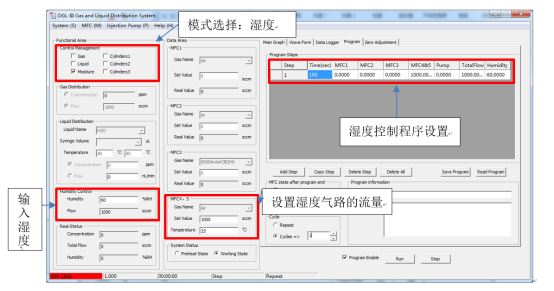
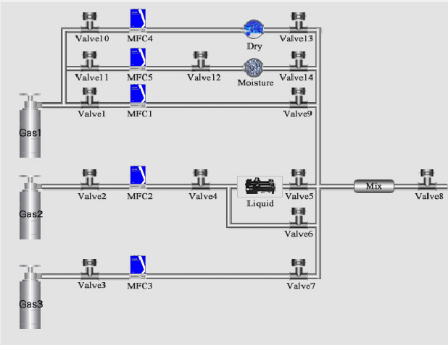
DGL-III moisture control benefits:
1. The dual-flow method is better than the moisture control equipment based on the principle of partial pressure method and ultrasonic method on the market. The equipment of partial pressure method or ultrasonic method produces macromolecular moisture, which is easy to produce macromolecular water mist, causing damage to the material, while the dual-flow method is the small-molecule moisture, which is relatively peaceful and uniform, and is more suitable for material research
2. Support long-distance testing (1.5m outside the equipment), the temperature and humidity probe is flexible and can be placed in different chambers
3. High-precision dynamic gas distribution (currently the highest in the industry, patent, exclusive), DHD-II and saturated salt solution method are difficult to get an accurate concentration of the atmosphere
4. Can accurately control the gas flow, support to control the humidity of different air sources
5. High index, the use of Rotronic high-precision temperature and humidity sensor probe, humidity control range: 2%RH-90%RH (extensible humidity range 0.5%RH~95%RH), accuracy ±0.8%RH, stability ±0.1%RH.
The limit index is related to the humidity and flow rate of the air source, and it is easier to achieve high humidity at a large flow rate, and it is recommended that the flow rate be generally controlled at 500-1000sccm.
3. Accessories consumables
a. Planar sensor substrate, Ag-Pd, Au, C electrode ceramic substrate sensor substrate, used for the moisture sensitive property analysis of the substrate.
Typical result
Complex impedance at different frequencies - humidity curve: indicates that the material at different frequencies, the corresponding complex impedance change size, usually the change of orders of magnitude, semi-logarithmic coordinates under the linear degree is the best working frequency.
Capacitance-humidity curve at different frequencies: indicates the variation trend of material capacitance at different frequencies, which is of great significance for device design, manufacturing process optimization, material modification and so on.
Wet hysteresis curve: measurement of the material from low humidity to high humidity, and then from high humidity back to low humidity, complex impedance difference. This describes the reliability of the device.
Response - recovery curve: Measures the time required for the material to respond to different humidity, the faster the response recovery, the better.
Complex impedance map: Measure the real and virtual values of the device output under different humidity and frequency, and establish a model to analyze the moisture sensing mechanism.
Humidity interference curve: Measure the characteristic change of the device under different humidity and analyze the water molecular interference.
Stability: The zero-point drift and sensitivity attenuation of the material are investigated for a long time.
SEM and TEM: describe the morphology and structure of the material. Generally, the structure with many tips and pores is considered to be conducive to the adsorption and deionization of water molecules.
reference
T. Nitta, Ceramic Humidity Sensor, Ind. Eng. Chem. Prod. Res. Dev., 1981, 20, 669-694.
E. Traversa, Ceramic Sensors for Humidity Detection: the State-of-the-art and Future Developments, Sens. Actuators B, 1995, 23, 135-156.
X.Q. Fu, C. Wang, H.C. Yu, Y.G. Wang, T.H. Wang, Fast Humidity Sensors Based on CeO2 Nanowires, Nanotechnology, 2007, 18, 145503.
L.J. Hong, M.J. Yang, Y. Li, A Novel Humidity Sensor Based on Carbon Black/poly(4-vinylpridine) Nanocomposite, Chin. Acade. J. Electr. Pub. Hou., 2006, 26, 39-41.
Cui Yu, Principle and Uncertainty Evaluation of Saturated Salt solution humidity Generator, Chin.Acade.J. Electr. Pub. Hou., 2007, 2, 29-33.